Технология производства керамогранита
Производство керамогранита можно разделить на четыре стандартных этапа:
• Замес
• Прессование
• Обжиг
• Обработка поверхности.
Замес. На первом этапе производства происходит подготовка смеси. Каолиновая глина смешивается с различными добавками, необходимыми для придания керамограниту нужного цвета или узора. На многих фабриках цех, в котором производится замес сырья, закрыт для посторонних, т.к. точный состав добавок и их пропорции составляют коммерческую тайну. Смесь, из которой изготавливаются плитки керамогранита, состоит из каолиновой глины, чистого кварцевого песка, полевых шпатов и различных красящих пигментов. Традиционно роль красящих пигментов выполняют окиси различных металлов.
В отличие от природного камня сырьевые составляющие керамогранита не являются источником повышенного радиоактивного фона. Поэтому мы хотим особо подчеркнуть, что керамогранит – это безопасный для здоровья материал.
Прессование. На второй стадии производства многое зависит от оборудования, на котором осуществляется формовка и прессование исходного материала. Современные прессы позволяют достигать давления свыше 500 кг на 1 см2. При таком высоком давлении внутри заготовки не остается пустот, частицы сырья спрессовываются до такой степени, которая позволяет обеспечить высочайшие потребительские свойства керамогранита. Именно на этапе формования обеспечивается достижение высоких показателей в линейных размерах (соблюдение размеров длины, ширины, толщины, параллельности сторон, прямоугольности, кривизны) в каждой плите. Минимальные отклонения в линейных размерах является одним из важнейших потребительских свойств керамического гранита.
Более новой технологией, принципиально отличающейся от прессования, является производство керамогранита методом экструзии. При использовании этого метода сырье под высоким давлением выдавливается в форму, с последующим обжигом и полировкой.
Обжиг. На третьей стадии производства закрепляются и усиливаются достигнутые при прессовании высокие характеристики полуфабриката керамогранита. По условиям технологического процесса температура и время обжига должны быть строго выдержаны, чтобы керамогранит не вышел "сырой" или "перегретый". Отклонения в технологическом процессе приводят к снижению прочности плит и различным деформациям. Обжиг проводится в длинной печи, сквозь которую проходит конвейер, на котором полуфабрикат транспортируется от пресса. Температура в печи достигает 1300 градусов. При такой высокой температуре внутри материала заготовки происходит завершение химических реакций и реструктурирование химических элементов. Сырьё спекается, образуя монолит. В результате, после охлаждения плитки, получается очень твёрдый непористый материал с близким к нулю показателем впитывания влаги и практически идеальных размеров.
Обработка поверхности. На четвертом этапе, после обжига, полуфабрикат перекладывается на полировочную или шлифовочную линию. Полировка производится конвейерным методом, в несколько этапов. При полировке применяются специальные пасты, изготовленные на основе алмазной пыли. В процессе полировки с плитки керамического гранита убираются мельчайшие неровности поверхности, и достигается высокий уровень зеркальности (до 80%). Настолько высокая степень полировки (плюс некоторые дополнительные мероприятия по уходу за керамогранитом) обеспечивает устойчивость керамогранита к различного рода загрязнениям - масляным пятнам, смолам, красителям и т.д. С поверхности, отполированной до такой степени, любые вещества смываются водой или подходящими химическими растворами без следа. Возможна более низкая степень полирования: до уровня зеркальности 20%. При этом поверхность становится на микроуровне менее ровной, отражательная способность плитки более низкая.
С целью получения шершавой поверхности плит керамический гранит не полируется, а шлифуется. После шлифовки плитка подвергается специальной обработке: либо покрывается глазурью, либо закаливается.
Подписывайтесь и будьте с нами:
Последнее изменение: 30.05.2013
Статья размещена ООО «Ф-31».
Похожие статьи
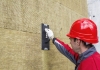
О том, как выбрать теплоизоляцию рассказывает Василий Аксенов
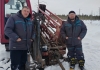
История становления ГНБ бизнеса. Риски и первые объемы!